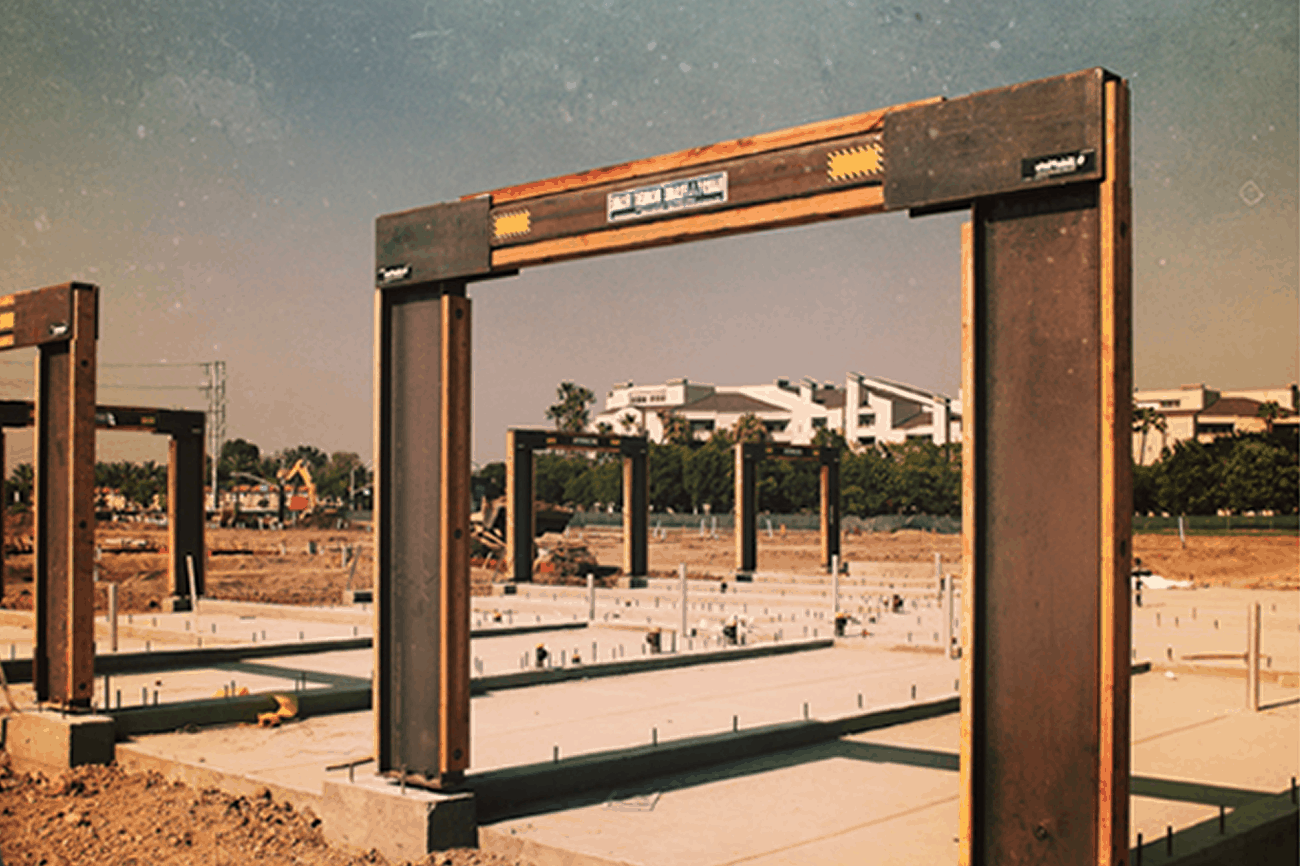
Lateral
Systems
LEADING IN LATERAL
NO OTHER SYSTEM
STACKS UP
The MiTek® Lateral Systems line is the only complete set of lateral force resisting products that meet all needs of the light-frame wood construction industry; from single family homes to multifamily complexes. The strength, stiffness, and ductility of the lateral load spectrum of solutions help maximize window and door openings without compromising structural integrity.
- Greater architectural freedom.
- Speed, quality, and cost-efficiency are attainable
- Trade friendly – and preferred by the trades!
The Complete Line of Lateral Solutions